Each quarterly issue has a central theme; however, other topics are also featured in each issue within the various Standing Columns listed below. Subject matter includes all application areas, techniques, concerns, and innovations related to shotcrete. With rare exceptions, specific product names are typically not.
Submit materials or questions to:
Cara Baker, Managing Editor | Email
Phone: (248) 973-7832
Shotcrete magazine contains these Standing Columns, and the topics that are typically covered under these column headings:
- Contractor Corner – helpful information geared towards the shotcreter, crew, or company.
- Editor’s Corner – magazine-related topics
- Goin’ Underground – related to tunneling, mining, caves, or other underground related topics.
- International – projects or shotcrete efforts outside of North America.
- Pool & Recreational Shotcrete Corner – related to pools, skateparks, or other recreational applications.
- Safety Shooter – safety-related topics.
- Shotcrete Corner – smaller project profiles, policy related/referenced articles.
- Shotcrete FAQs – questions answered by ASA’s technical team. Submit a question here.
- Sustainability – related to sustainable topics in shotcrete.
- Technical Tip – technical perspectives on materials, equipment, or processes.
- Women in Shotcrete – nominate a woman who is making her mark on the shotcrete industry with this simple form: https://shotcrete.org/women-in-shotcrete-application/
ASA also endeavors to choose an article from each issue, deemed most relevant for shotcreters, to be translated into Spanish.
What to include when submitting materials for feature articles or columns:
- Article text in Microsoft Word (suggested average article length is 1500 to 2000 words, and project report length is 800 to 1000 words)
- Four or more illustrations preferred (photos, tables, charts, figures, drawing details, etc.)
- Sent as separate attachments as well as embedded in the places you want them referenced in the article.
- Illustrations should complement the article in some way
- Illustrations should be accompanied by captions (12-15 words or less)
- Illustrations should be placed in the article and cross-referenced appropriately by the author (see Resources)
- Photos should be 300 dpi minimum and in .png or .jpg format
- Sent as separate attachments as well as embedded in the places you want them referenced in the article.
- Technical information should be accurate and checked by the author:
- Measurements (including length, weight, volume, area, speed, etc.) must be in U.S. units followed by metric conversion in parentheses
- Temperature must be in degrees Fahrenheit followed by degrees Celsius in parentheses
- Full references (for sources cited) should be listed and properly formatted (see Resources)
- Short Author Biography (approximately 100 words)
- Author photo (Headshot-style, 300 dpi minimum, .png or .jpg)
Member Benefits
Sustaining & Corporate Members enjoy the exclusive, ongoing opportunity to be featured in several regular columns:
Each issue provides an occasion to feature both a Sustaining and a Corporate member in a two-page profile, respectively. These pages allow companies to share their histories, product offerings, personnel highlights, sample project listings, or most anything they wish to highlight about their company. Sustaining members have this opportunity once every five years, while corporate members enjoy this benefit once every ten years.
What to include when submitting materials for Sustaining Corporate or Corporate Member Profiles:
- Article text in Microsoft Word (suggested average length is 500 words)
- Up to two pages of content
- Company Contact information (full name, contact person(s), address, phone, fax, and website information)
- Accompanying photo(s): 300 dpi, PNG or JPG format and corresponding caption
- Company logo: Vector file (EPS) preferred; 300 dpi PNG or JPG format otherwise
News items appropriate for this column include new products, ventures into new market segments, applications for current products, approvals, or research.
What to include when submitting materials for New Products & Processes:
- Article text in Microsoft Word (suggested average length is 200 to 300 words)
- Contact information (website, email, phone number)
- Accompanying photo(s): 300 dpi, PNG or JPG format and corresponding caption
- Company logo: Vector file (EPS) preferred; 300 dpi PNG or JPG format otherwise
News items appropriate for this column include awards, personnel changes, new location, new logo, new website or social media platform.
What to include when submitting materials for Industry News:
- Article text in Microsoft Word (suggested average length is 200 to 300 words)
- Contact information (website, email, phone number)
- Accompanying photo(s): 300 dpi, PNG or JPG format and corresponding caption
- Company logo: Vector file (EPS) preferred; 300 dpi PNG or JPG format otherwise
Shine a light on individuals or crews for noteworthy performances.
- Article text in Microsoft Word (suggested average length is 500 words)
- Up to two pages of content
- Accompanying photo(s): 300 dpi, PNG or JPG format and corresponding caption
- Company logo: Vector file (EPS) preferred; 300 dpi PNG or JPG format otherwise
- Company Contact information (full name, contact person(s), address, phone, fax, and website information)
Content: Please e-mail article text, author biography text, and caption text as a Microsoft Word document.
Photos/Graphs: High-resolution (300dpi minimum) digital images, preferably sized at a minimum of 4 x 6 in. for general photos and at 1-1⁄4 x 1-3⁄4 in. for author photos, can be submitted via e-mail, as a google drive link, or as a dropbox link (provided by the author).
Logos: Vector EPS files if possible; 300 dpi PNG or JPG format otherwise.
We are unable to accept the following:
- Printouts or copies of photos
- Embedded graphics (due to low resolution issues)
Article authors will be asked to sign a copyright release prior to publication.
All concrete materials, including water, are thoroughly mixed and introduced into the delivery equipment. The wet concrete is pumped to the nozzle where compressed air is added to provide high velocity for placement and consolidation of the material onto the receiving surface.
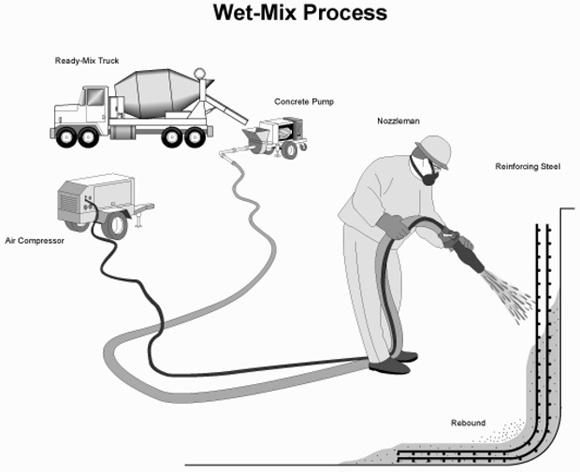
Framing Smartphone Photos for Shotcrete Jobs Using the Rule of Thirds
With the improvements in smartphone technology over the last decade, many of the phones we have in our hands are just as good at taking quality photos as some point-and-shoot cameras. In the absence of a professional photographer to follow us around and shoot pictures at our job sites, it turns out we have the next best thing in our pockets!
The Jetcreter – The First Continuous-Feed, Dry-Mix Gun
During the summer of 1970, on my 18th birthday, my father woke me up and told me they needed me on a job. I drove out that morning in July to the Crucible Specialty Steel plant in Midland, PA. It was my first experience working on a Gunite job. We were gunning refractory in a vessel, and I was throwing 100 lb (46 kg) bags of pre-packaged refractory into a paddle mixer to pre-dampen the material. We emptied the paddle mixer on sheets of plywood and shoveled the pre-dampened refractory material into the dry-mix shotcrete gun’s hopper. The Jetcreter was a continuous-feed gun, and it was tough for us to keep up with it. It was a very long day for me because it took 15 hours to complete the gunning. I left the house that morning in the dark and returned home in the dark. That was my introduction to “Gunite” (now referred to as dry-mix shotcrete).
Coastal Gunite Construction Company Celebrates 40 years in Business
Coastal Gunite Construction Company delivers shotcrete construction services to build, maintain and rehabilitate concrete structures. Founded in 1983, Coastal Gunite Construction Company has developed a reputation for quality, integrity, and meeting strict performance requirements for both large and small projects. Their specialized experience in structural shotcrete construction allows them to provide owners and project engineers with cost-effective and enduring solutions to concrete infrastructure construction and maintenance needs.
High-Production, Quality Shotcrete
High-production shotcrete projects are amazing to observe; when operating at optimum level, it appears to be very simple. Those of us in the shotcrete industry know better; there are many well-trained people and detail-based processes required to make it all happen. The following is a brief layout of what it takes to operate as a high-production shotcrete contractor while producing the highest quality product.